ソリューション
適用パターン1:得意先から出荷精度の向上を求められた!
![]() |
受注票やピッキングリストを使いながら目視で品揃及び検品を行っているが出荷ミスが起きてしまう。 |
![]() |
ハンディを用いて、ピッキング検品を行うことで、実際の出荷予定データと照合しての検品が可能!ピッキング作業はリストで行って、最終的にハンディを用いて出荷検品を行うことも可能です! |
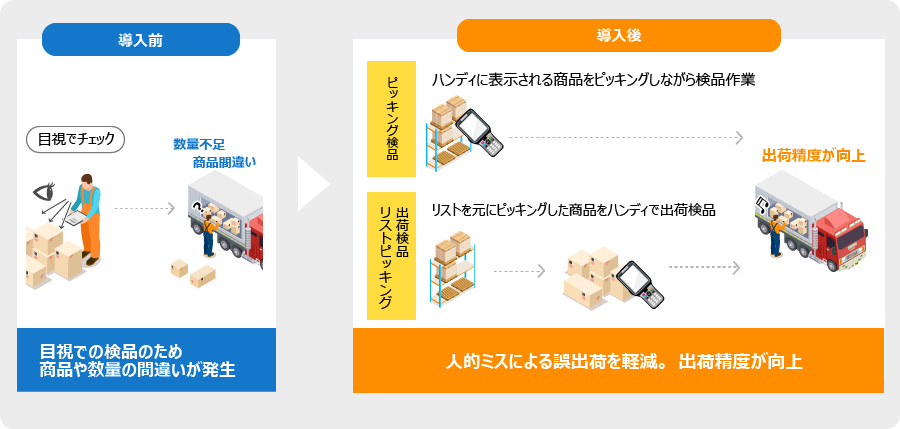
![]() |
ロケーション管理ができていないので、品揃えするのに非常に時間がかかる。 |
![]() |
LogiLiteでは固定ロケーション管理が可能になっておりますので、ピッキングリストをロケーション順に出力します。よって、作業者はピッキングリストの順番で品揃えを行うので無駄な移動を無くし、作業効率UPが可能です! |
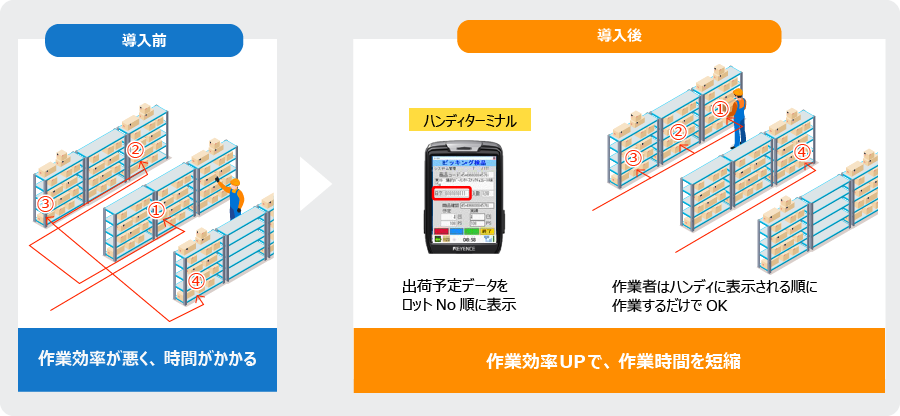
適用パターン2:既存の販売管理システムと実際の倉庫在庫が一致しない!
![]() |
販売管理など基幹システムの在庫管理では、仕入・売上といった伝票処理をもとに在庫管理を行います。それらは在庫数を把握するだけであり、入出荷やピッキングといったモノの流れはサポートされません。その為、あるタイミングでは販売管理上の在庫と実際の倉庫在庫が一致しないといった事態が起こりえます。 |
![]() |
倉庫作業をサポートするLogiLiteと連携ハンディターミナルを活用することで入荷から出荷までのモノの流れをリアルタイムかつ正確に記録・管理することができます。必要に応じて基幹システムと各種データ連携させ、システム間の在庫不一致の解消に貢献できます。 |
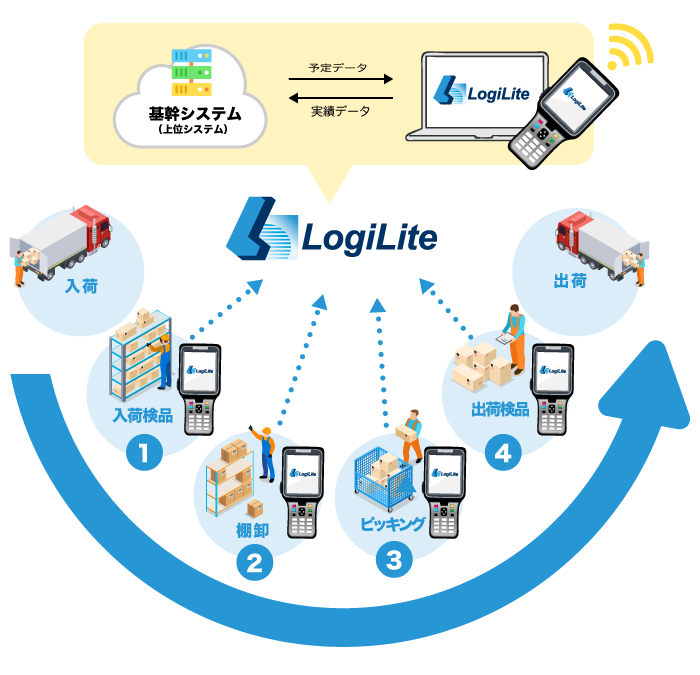
1.入荷検品 | 発注データ通りに商品が入荷されているかチェックします。 |
2.棚卸 | 在庫数量がデータ通り存在するかをチェックします。 |
3.ピッキング | ピッキング指示データをもとに必要な商品を棚から集めます。 |
4.出荷検品 | 出荷予定データの通りに出荷先ごとに商品が用意されているかをチェックします。 |
適用パターン3:紙ベースでの棚卸作業が非常に煩雑である!
![]() |
紙の棚卸表を使い目視で作業を行っている場合、記入ミス・商品の判別ミス・数え間違いが発生しやすい状態といえます。 また棚卸結果を基幹システム等に入力する必要がある際は転記ミスの原因ともなりえます。 |
![]() |
Logi Liteと連携ハンディターミナルで作業を行うことで、記入ミスやパソコンへの打ち込みミスの撲滅に貢献。 データはハンディターミナルから直接転送されるため、パソコンへの打ち込み作業自体が不要です。 |
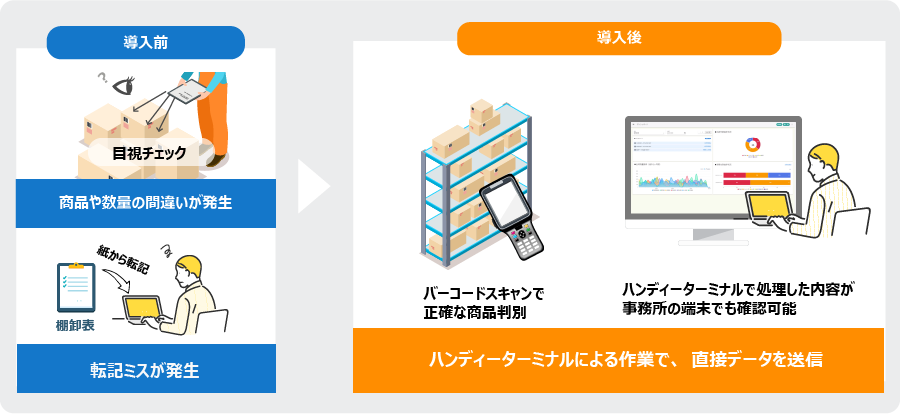
![]() |
また一斉棚卸のほか、循環棚卸も可能なため、全体の作業を止めずに一部のエリアのみ棚卸することもできます。 |
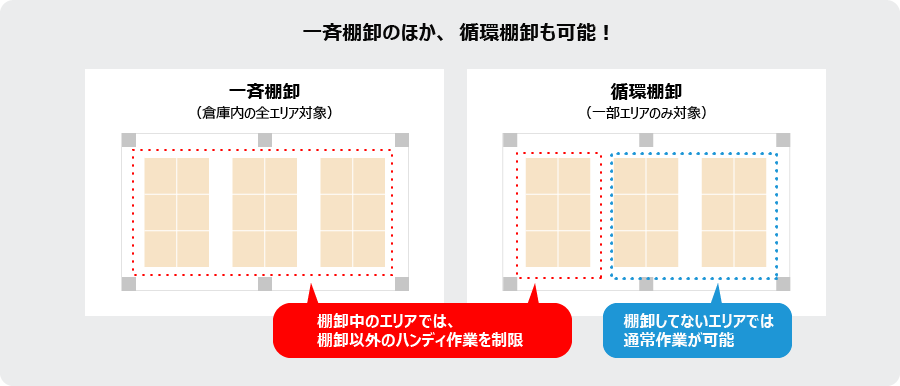